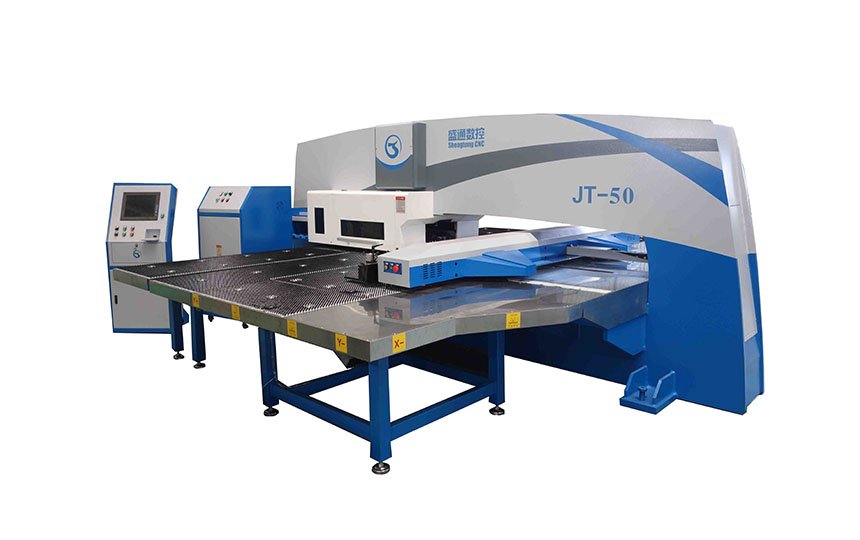
Mechanical CNC Punch Press
The STON mechanical CNC punch press offers significant advantages such as energy efficiency, excellent stability, high tonnage capacity, and competitive pricing. It is equipped with 32 turret stations as standard, including 2 rotating stations, allowing for diverse operations such as punching and drawing.
The Mechanical CNC Punch Press combines the precision of computer numerical control technology with the reliability and durability of mechanical drive systems.
Inquiry Now
add to cart

··· STON Mechanical CNC Turret Punch Press ···
Model:STSK-JT30/STSK-JT50
Punching Force:30/50tons
Parameter | Unit | Remarks | ||||||
Model | STSK-JT30/STSK-JT50 | |||||||
Punching Force | 300(30)/500(50) | KN(T) | ||||||
Frame Structure | O-Type Closed Frame | |||||||
Max Sheet Size for Single Positioning | X-Axis2500 Y-Axis1250/1500 | mm | Customizable to Non-Standard | |||||
Max Sheet Thickness | 6 | mm | Based on Sheet Type | |||||
Max Punching Diameter in a Single Stroke | φ88.9 | mm | Customizable to Non-Standard | |||||
Max Punching Frequency | 280 | hpm | ||||||
Max Punching Hits | 280 | hpm | ||||||
Number of Control Axes | 4(X、Y、T、C) | piece | ||||||
Die Type | Long Guide 85 Series International Standard Die | |||||||
Turret Station Distribution | 16A、11B、3C、2D(Including Rotary Stations1B、1C) | Standard | Customizable to Non-Standard | |||||
Repositioning Cylinder | 2 | set | ||||||
Number of Clamps | 2 | piece | ||||||
Max Feeding Speed | X-Axis90 Y-Axis80 | m/min | ||||||
Worktable Structure | Brush and Universal Ball Composite Work Surface | |||||||
Max Turret Speed | 40 | rpm | ||||||
Processing Precision | ±0.1 | mm | ||||||
Max Load Capacity | 150 | Kg | ||||||
Total Power Consumption | 3 | Kw | ||||||
Air Source Pressure | 0.55 | Mpa | ||||||
Power Supply | 380±5% | V | ||||||
Overall Dimensions | 5000/5500×5200×2100 | mm |
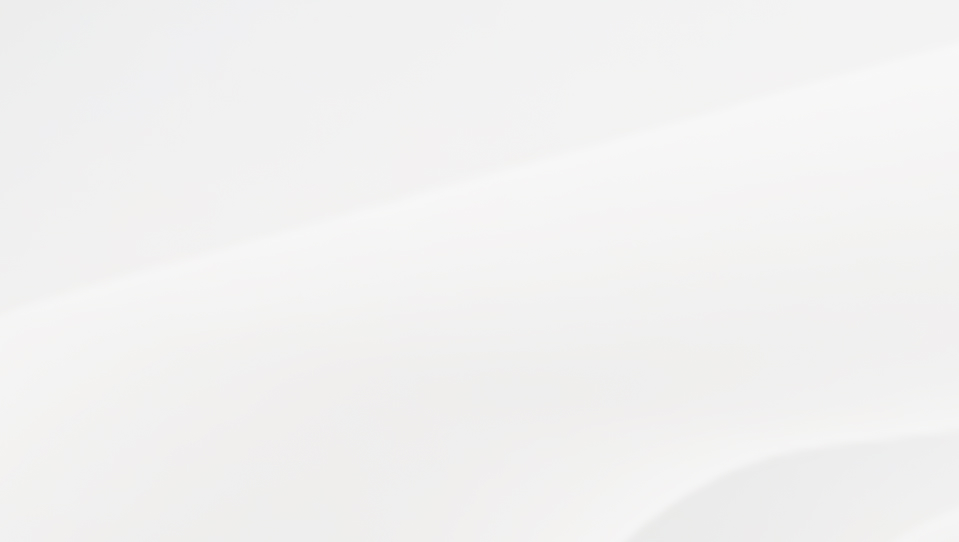
Overview
The STON mechanical CNC punch press offers significant advantages such as energy efficiency, excellent stability, high tonnage capacity, and competitive pricing. It is equipped with 32 turret stations as standard, including 2 rotating stations, allowing for diverse operations such as punching and drawing.
Learn more
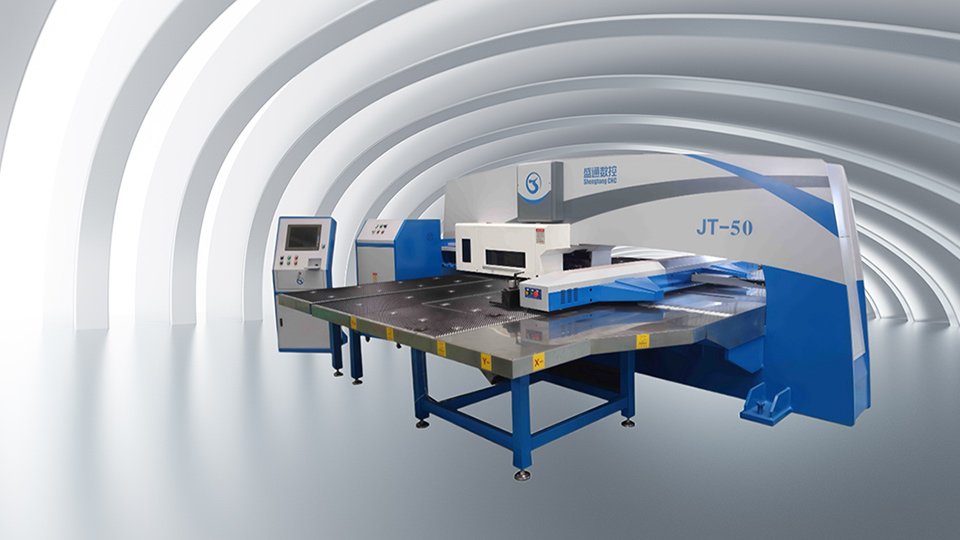
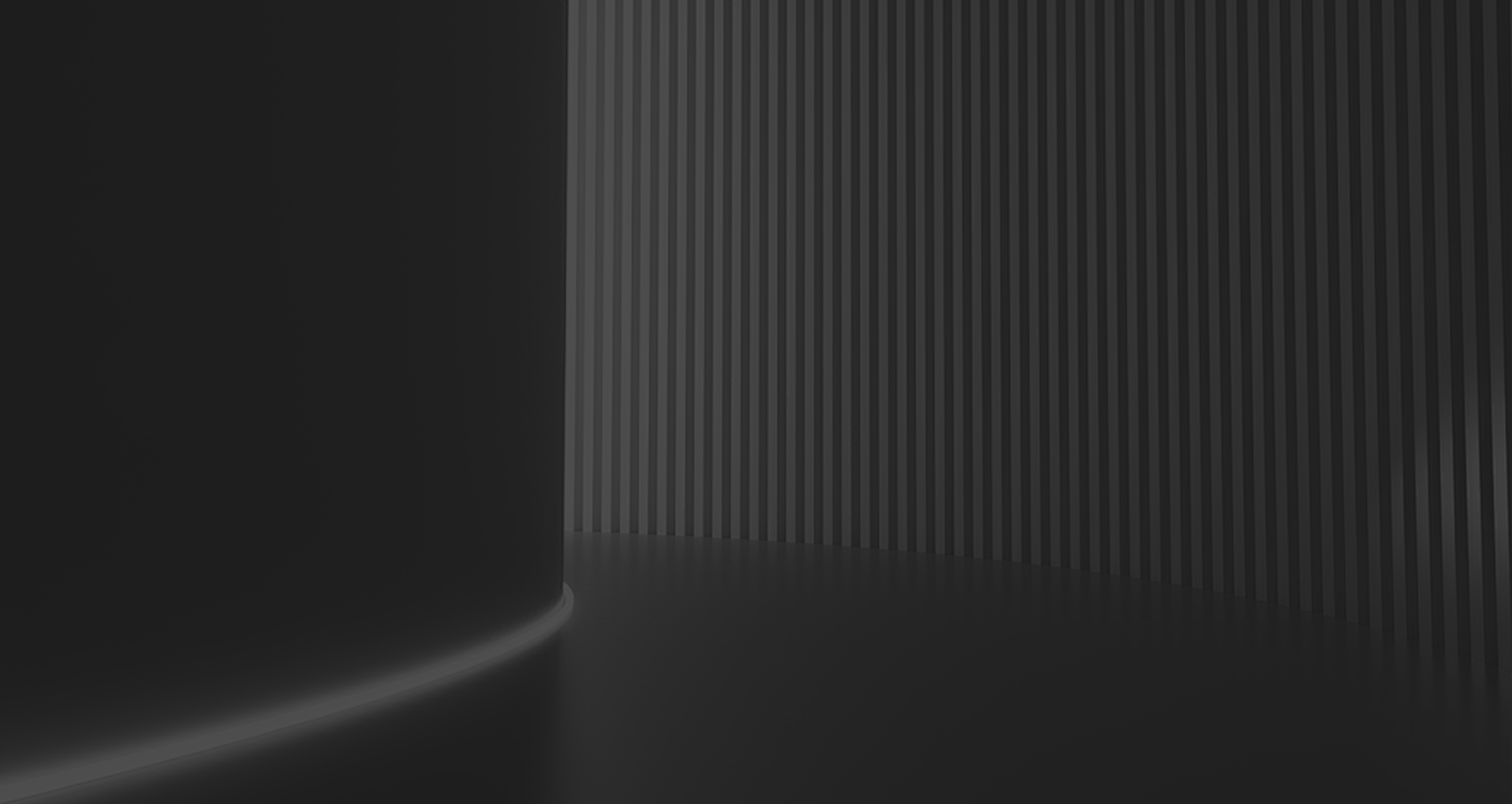
Punching Demonstrations
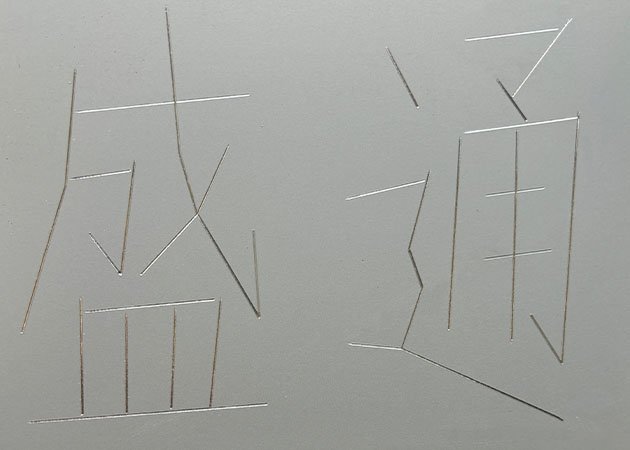
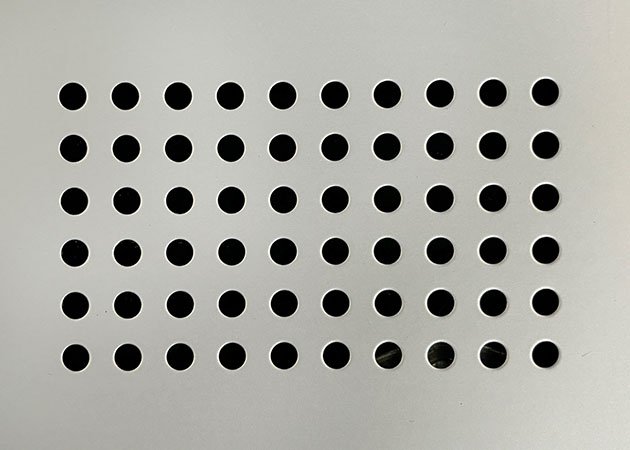
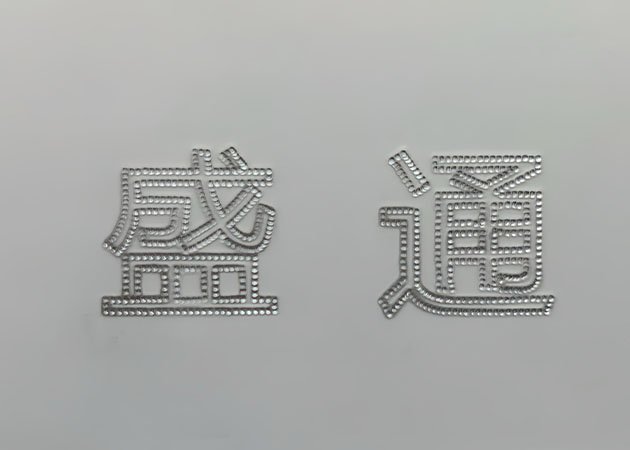
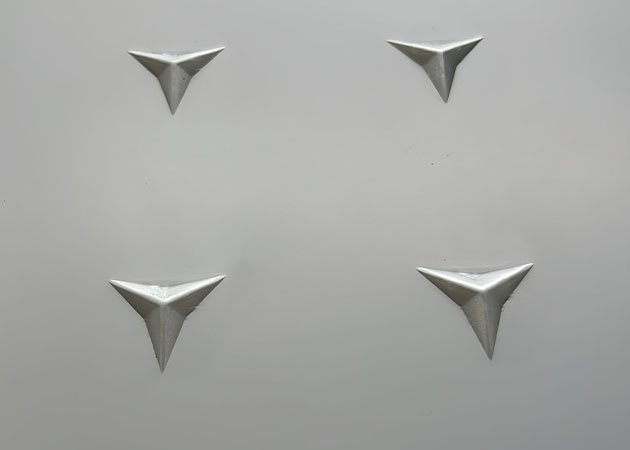
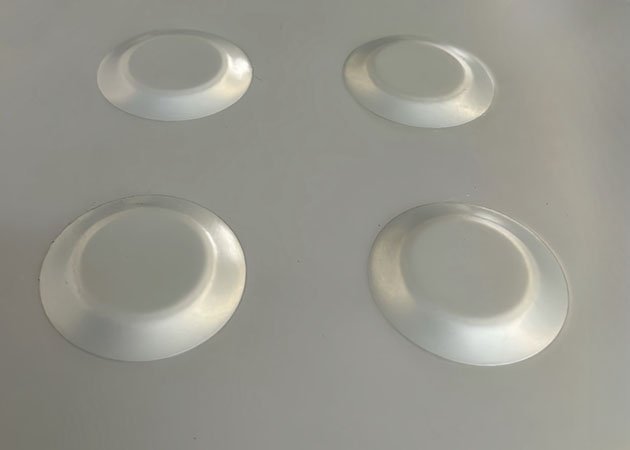
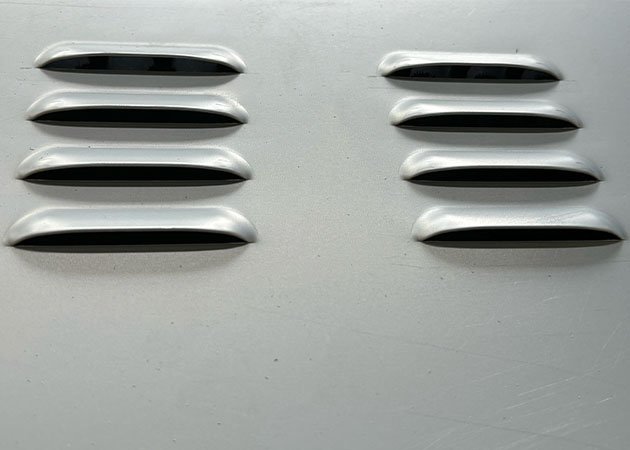
Industry Applieation Cases
-
Furniture Side Panel
watch the process
-
Garden Fence
watch the process
-
Patterned Curtain Wall
watch the process
-
Showroom Building Facade
watch the process
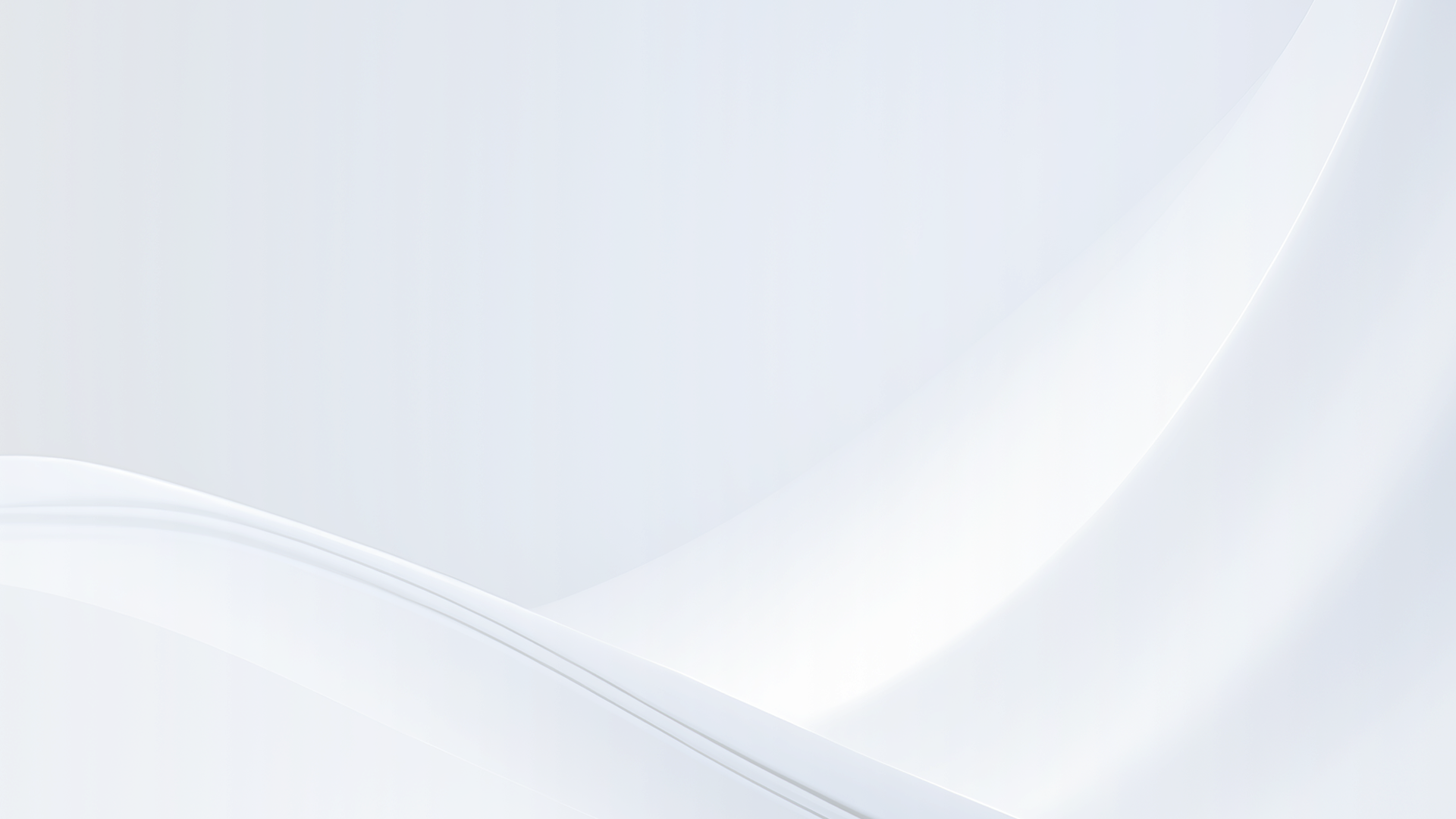
Case Show
-
AC Unit Enclosure
-
BBQ grill
-
Building curtain wall
-
Highway Sound Barrier
-
Air conditioner
-
Aluminum Cladding Panel
-
Cabinet Enclosure
-
Filing cabinet

··· check your industry match ···
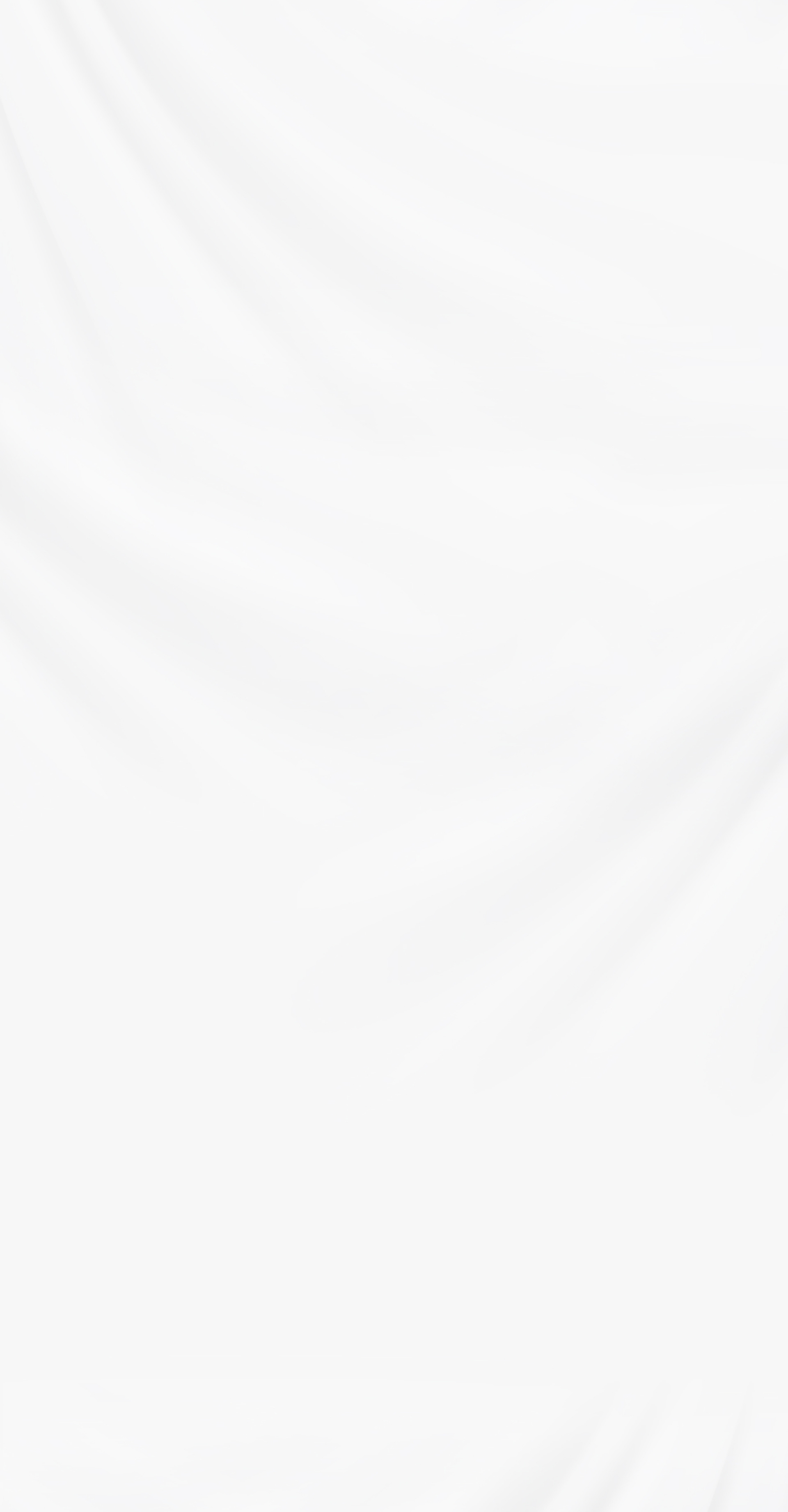
Component Introduction
-
01.
Key Features
•High-efficiency Punching: Utilizes flywheel energy storage for consistent, stable impact, ideal for mass production.
•Cost-effective: Low equipment cost, simple structure, easy maintenance, and low operational expenses.
•Ultra-low Energy Consumption: As low as 3 kWh per hour, significantly reducing production costs.
•Multi-station Turret: Supports rapid tool changes, reducing downtime and improving productivity. -
02.
Flywheel System
•Powerful Output: Proprietary flywheel system offers consistent power, reducing motor load and ensuring high-speed continuous production.
•Optimized Energy Efficiency: Flywheel design minimizes energy consumption while maintaining stable operation. -
03.
CNC System
•Precision Control: Employs pulse control technology for precise, consistent punch control.
•Efficient Programming: Supports G-code and graphical programming for ease of use and error reduction. -
04.
Frame Structure
•High-strength Design: "O"-type closed structure, with finite element analysis ensuring high stability and vibration resistance.
•Precision Machining: The frame undergoes high-temperature annealing to eliminate internal stress. The entire structure is machined in a single fixture setup, ensuring optimal assembly accuracy. -
05.
Transmission Mechanism
•Mechanical Transmission: High-precision system ensures stable punching and extends equipment life.
•Easy Maintenance: Simple, reliable design for easy upkeep, improving long-term operational efficiency. -
06.
Feeding System
•High-precision Feeding: X, Y-axis guides and lead screws are integrated, ensuring precise material handling. Pneumatic clamps enhance stability.
•Lubrication System: Multi-point automatic lubrication ensures sufficient lubrication, reducing wear. -
07.
Safety and Maintenance
•Safety Design: Equipped with multiple safety features such as emergency stop buttons and fault detection systems for operator safety.
•Simplified Maintenance: Optimized design reduces daily maintenance requirements, minimizing downtime and enhancing overall productivity.